Metal Plating, Coating & Finishing Services
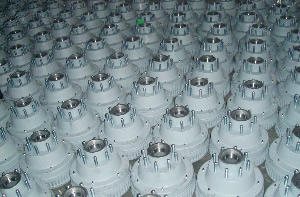
In the market for strong, rugged, and reliable metal plating, coating, and finishing services for your forged, cast, and extruded parts? To provide the best value and protection available, DEECO offers Metal Coating Services, Metal Surface Finishing, Plating Services, Machined Parts, and Metal Stamping for all the products we manufacture. To ensure the best quality service and results, we only provide metal coating, plating, and finishing services to the forgings and extrusions that we supply.
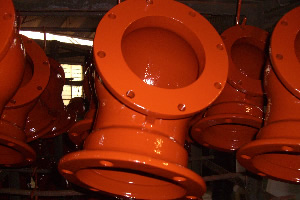
To learn more about our exclusive metal finishing, plating, and coating processes, or for more information on our additional secondary services, please contact or call us at 1-800-272-7784. Our technical team will work with you to determine the best options based on your project’s specifications.
Metal Plating
Metal plating services utilize a thin layer of metal that covers the substrate of an existing metal. The metal plating process provides significant advantages for applications looking to gain the beneficial attributes of multiple metals. DEECO provides plating services for the following materials:
- Silver
- Electroless and electro-deposited nickel
- Chrome
- Gold
- Tin
- Zinc & zincate
- Dry film
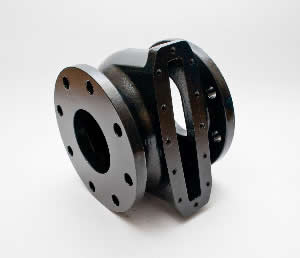
Metal Coating
Metal coating services for forged, cast, and extruded parts provide advanced protection against corrosion and extended wear in challenging conditions. Metal-coated forged, cast, or extruded parts benefit from extended wear resistance protection, prolonging part life expectancy. DEECO offers the following metal coating processes:
- Conventional anodizing
- Aluminum hard-coat anodizing
- Arkema Rilsan® nylon powder coating
- Black oxide
- Phosphate coating
Metal Finishing
Precision metal surface finishing services provide protection from corrosion and harsh environments for cast, forged, and extruded parts. DEECO offers the following metal finishing services:
- Passivation
- Silk screening
- Shot blasting
- Masking and plugging
- Paints, primers, and top coats
- Tumbling
Machining
DEECO offers several machining services to support your part and component processing needs. Whether your part requires turning, drilling, milling, or any other machining operation, DEECO provides the processing services your project requires. DEECO precision machining services include:
• Turning | • Grinding |
• Drilling | • Honing |
• Milling | • Lapping |
• Single-point cutting | • Ultrasonic |
• Shaping | • Abrasive Jet |
• Planing | • Chemical |
• Boring | • Torch cutting |
• Broaching | • EDM |
• Sawing | • High energy beam |
Metal Stamping
Metal stamping service processes generally involve single-stage or multi-stage operations. These processes require a die/tool that utilizes a single stroke or multiple strokes to produce the desired form or part from the strip or sheet metal. DEECO custom metal stamping services include:
- Stamping
- Punching
- Blanking
- Embossing
- Flanging
- Bending
- Coining
Additional Services
DEECO Metals also provides the following services based on customer needs and project specification requirements:
- All engineering services to obtain the best costs, suggesting the best metals and alloys suited for your product, assistance with the best manufacturing processes to produce your products, etc.
- We offer all types of Machining equipment available to produce your product.
- We also offer coatings and surface treatments, like dip, hand and spray painting, polishing, powder coating, anodizing, shot-blasting, vibratory finishes, etc.
- Assembly services of complete products or sub-assemblies.
- Special custom Packaging to customers’ requirements and special printing of Co. name, logo, etc.
- We offer stocking programs at our warehouse, such as JIT (Just In Time) and Kanban programs to meet your lean manufacturing incentives.
The DEECO Metals Advantage
With 38 years of industry expertise, DEECO Metals is your trusted source for precision metal plating coating, plating, and finishing services for your forged, cast, and extruded part needs. DEECO is proud to be your one-stop shop for premium investment castings, sand castings, die castings, forged parts, extruded shapes, machined parts, stamped components, and much more! To ensure our customers are fully backed on every front, DEECO also offers the following support services:
- Front-to-back technical support
- Warehousing
- Sales support
- Fixed order pricing
- Assembly
Our ultimate objective is to help you increase your profit margins by reducing your overall production costs, saving significant time and money!
Contact DEECO for Precision Metal Plating, Coating & Finishing Services Today
Searching for the industry’s most comprehensive metal finishing, coating, and plating services? DEECO Metals is your trusted partner for precision forged, cast, and extruded part protective finishing. Contact us for more information, or check out our photo gallery for examples from past projects.