Casting vs. Extrusion vs. Forging
When it comes to manufacturing metal parts and components, there are often multiple ways to achieve the same end result. Casting, extrusion, and forging, to name a few, are all reliable methods of producing metal products. Each has its own unique capabilities and pros and cons. Which is the best option for manufacturing your parts at the best possible costs?
What are Metal Castings?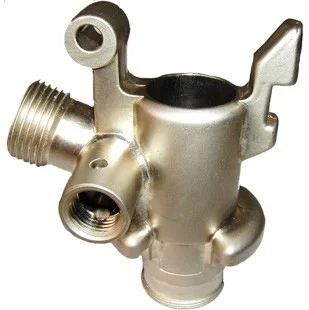
In some casting methods, metal in ingot or scrap form is heated until it reaches a molten state and the right specifications. Once they have achieved this, the molten metal is poured into a prepared sand cast mold; or injected into a custom tool steel mold for die casting; or an aluminum or steel die for investment casting to achieve the desired design required. The molten metal immediately cools in the sand mold or die and solidifies into the desired cast metal part required. Some castings may require machining and/or a surface finishing to obtain the final required part.
What are the Types of Castings?
While there are several different casting methods, die casting, sand casting, and investment casting are the most commonly used. To achieve the best suited and most cost-effective casting method, one must consider the metal or alloy to be used, the dimensions, the geometry, the weight of the part and the quantity. Every casting method uses a different process to deliver an acceptable cost-effective part.
In general, casting is the preferred method used to produce complex geometrical industrial metal parts. Molten metal flows much like a liquid so it therefore completely fills all areas of a complex mold design to achieve the exact part required. This also makes casting the best choice for parts that need internal cavities or voids, such as valve and pump bodies.
With certain exceptions at the extreme ends of the spectrum, there are no size limits for a sand casting as most other methods have limitations. Some Casting Methods can also maintain very high dimensional accuracy. a near net shapes as well as very good surface finish. Industry-standard tolerances do increase with casting size and the casting process.
What are the Advantages and Disadvantages of Metal Casting?
PROS of CASTING |
CONS of CASTING |
Holds tighter tolerances in complex part designs. With some processes, very thin wall thickness |
May result in internal porosity, unintentional surface voids, and other imperfections |
Produces complexed design parts along with cores or voids. The cast part requires less machining than some other manufacturing methods |
If required, parts are not as tough as those created by other processes, such as forging and have a lower impact & pressure resistance |
Generally lighter than otherwise-identical parts produced by other methods and therefore less expensive. Some processes have a very good surface finish so less preparation for coating |
Generally requires close operator supervision to ensure the best quality. Sand casting does not provide the best surface finish |
Part design modification to dies or molds is faster, easier and less costly. |
May require more machining in critical areas of the part |
What are Metal Extrusions?
The extrusion process involves using a high-pressure press that forces a metal billet through an outlet, called a die, which is smaller and/or a differently-shaped cross-section that matches the desired shape of the bar or extruded shape required. A nearly unlimited number of cross-sections can be produced using the extrusion method.
The resulting profile can be as long as is necessary. In some cases, where small parts are made from the shape, the profile is cut into shorter lengths. More than any other metal forming process, the extrusion process creates various mechanical properties which may be required in the final part being produced. The process produces elongated grain structure that increases the raw material’s mechanical strength.
What's the difference between Hot and Cold Extrusions?
Hot extrusion, with the metal above its recrystallization temperature, it helps eliminate pores and voids in the material, breaks up inclusions in the raw metal that can cause weakness, and recrystallizes the material into a finer grain structure. This process produces lengths of Barstock or Profile (shape) bar.
Cold extrusion, with the metal at ambient temperature, imparts a better surface finish and further strengthens the part via strain hardening. Cold extrusion also allows for greater geometric accuracy on smaller short lengths of a part produced by this method.
What's the difference between Direct and Indirect Extrusions?
For direct extrusion, the material is pushed through the work chamber by a ram and extruded through an outlet (Special Steel Die).
For indirect extrusion, the material is completely contained in the chamber and the outlet is built into a hollow metal ram or it forms over the ram. So as the ram pushes into the material, the profile is extruded into and through the ram itself or over the ram. This method is used a lot for tube-shaped lengths.
As with casting, the proper extrusion method for a given project is determined by the material/alloy being extruded and the dimensions and geometry of the final part.
What are the Advantages and Disadvantages of Extrusions?
PROS of EXTRUSION |
CONS of EXTRUSION |
Ideal for near net shape in long lengths. Used in the length, like a hand Rail or cut into short pieces to be machining into parts |
Can result in surface oxidation (oxide scale) and needs to be removed by acid or mechanical methods |
The near net extruded shape yield low scrap from machining the parts. This material has a very homogeneous cross-section especially for parts requiring mechanical properties & pressure tightness |
If not controlled, susceptible to surface cracking, internal cracking and surface lines from bad maintained dies |
Therefore, the resulting grain refinement improves the material’s impact resistance, ductility & strength |
Limited part complexity |
Fast & efficient for high volumes |
What is Metal Forging?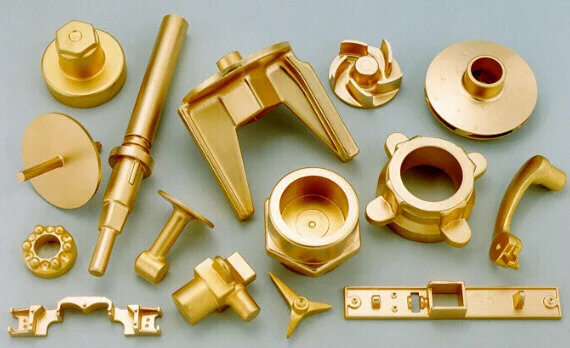
Forging uses massive amounts of compressive force to press a solid piece of metal (billet) into the desired shape or part. Under pressure, the raw metal (billet) is forced into a custom produced special steel die that is made into the desired shape. In general, although mechanical strong, forged parts require more machining to achieve the required final part.
What are the different Forging Methods?
A variety of forging methods exist, classified by the process temperature (cold forging or hot forging, referring to the forged metal’s temp) and the style of die used (open-die forging or closed-die forging). As with casting and extrusion, the most effective forging method for a particular project depends on the metal or alloy being forged, as well as the intended application of the final parts.
In general, forging produces parts that with excellent mechanical strength, impact strength, shear strength, and wear resistance. This is due to the high pressure the raw metal materials are put through and the resulting deformation, which causes metallurgical recrystallization and grain refinement that conforms to the part shape.
What are the Advantages and Disadvantages of Forging
PROS of FORGING |
CONS of FORGING |
Greater structural integrity & mechanical strength due to altered grain structure of materials |
Difficult to meet tight tolerance requirements, unless close die forging |
Less material scrap & reduced labor requirements. Close die forging can have some coring to reduce weight and costs. |
Significant secondary processing may be required to achieve final design specifications on open die forging |
Eliminates surface porosity & internal cavities and voids. Close die has good surface finish |
Nature of the open die forging method is not conducive to complex or intricate part shapes |
High reliability & consistency in ductility, strength & yields. Close die has near net shape |
Contact DEECO Metals for your complete metal shop needs
DEECO Metals is your leading resource for custom architectural metal castings. Request a quote today or contact us to learn more.