Metal Extrusions
At DEECO Metals, we bring over 38 years of expertise in metal manufacturing to deliver high-quality custom metal parts that support essential systems around the globe. We are committed to providing quality custom extruded profiles in a variety of alloys to those with the vision to see the potential of these materials.
Our custom extruded shapes are supplied in copper & copper based alloys (brass & bronze), nickel silver, pink bronze and stainless are also available. Complex custom extruded shapes can be fairly easily produced in aluminum, but are considerably more difficult in brass or bronze or copper and even more difficult in stainless. DEECO's mills state-of-the-art equipment helps supply some of the most complex custom extruded shapes in the industry in sizes from very small to very large.
Our engineers will use their expertise, in manufacturing and materials, to recommend the ideal material from both performance and a cost standpoint. We are committed to excellence and adhere to the highest industry benchmarks We also offer precise tolerances, consistency of product, reliable service and a reputation for problem-solving, all supported by extensive research and experience.
To save 10-20% over your current supplier, send us your extrusion samples or drawings.
Custom Metal Extrusion Products
- Plumbing parts and fittings
- Valve, pump, tap and faucet fittings
- Decorative shapes
- Door and lock parts
- Window and door frames
- Elevator cab and landing sills
- Large heavy industrial uses
- Electrical components from sockets and contacts
- Highly complex electrical switchgear
- General engineering
- Cold-formed brass screws
- Machined components requiring precision tolerances
- Precision engineered doors and window suites
- Handrails and balustrades
- Fishing lures and other sports and recreation
Standard Metal Profiles with Complex Shapes
DEECO can provide the standard profiles or simple profiles you need along with your custom metal extrusions. Save time and money by requesting your t slot extrusions, v slot extrusions or other standard profiles from DEECO Metals along with your quote for custom metal extrusions.
Common Extrusion Materials
Brass Extrusions
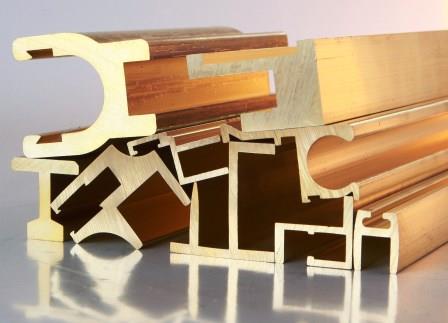
In its basic form Brass is an alloy of copper and zinc, but most alloys contain additional elements. For architectural purposes Brasses are widely used, however, the building industry commonly refers to some of these alloys as Bronze; although it is a misnomer, it is accepted practice.
Bronze Extrusions
In its basic form Bronze is an alloy of copper and tin. Within architectural applications, true bronze is rarely used. In the USA we refer to Architectural Bronze extruded shapes even though it is a brass.
Nickel Silver Extrusions
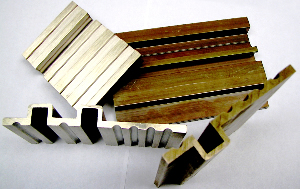
In its basic form, Nickel Silver is an alloy of copper, nickel, and zinc, which has a warm silver appearance.
Stainless Steel Extrusions
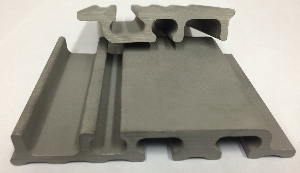
The durability and natural corrosion resistance of stainless steel make steel extrusions well-suited to tasks in harsh environments, while its distinct look makes them ideal for decorative purposes.
Using Alloys for Extrusions
Copper alloys possess different properties and as a result, have varied uses. Some alloys are used for casting, some for extrusion and hot forging, and others for sheet and strip manufacturer.
Across the range of alloys, a number are used for manufacture in more than one condition; for example, a given alloy may be capable of being used for both casting and extension.
The appropriate use of Brass alloys and Bronze alloys can result in an over-all color matching system which is important in architectural applications.
Colors of Metal Extrusions
General
Natural Color
Create Your Custom Metal Extrusions Today
Contact us for more information on our custom metal extrusions, email sales@deecometals.com, or request a quote today. You can also contact us at 1-800-272-7784 to speak to a technical sales representative, or to schedule a full consultation.
To help ensure your parts are of the highest quality, we also offer design, metallurgical, and technical assistance. We welcome your orders and promise superior service and quality.