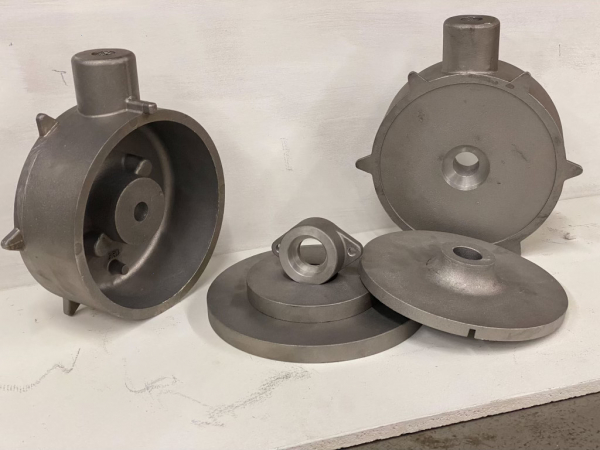
Gravity Casting
Gravity casting, or permanent mold casting, is a cost-effective production method for high-volume manufacturing of small, simple metal parts with uniform wall thickness. DEECO Metals offers mill run gravity casting capabilities to meet your project requirements.
Request a quote or contact DEECO Metals to learn about permanent mold casting, reusable aluminum casting molds, and our other metal casting capabilities.
Permanent Mold Casting Production Capabilities
Permanent mold castings are typically used for medium to high-volume production of small, simple metal parts with uniform wall thicknesses. Non-ferrous metals are usually used in this process, such as zinc alloys, aluminum alloys, magnesium and copper alloys (brass alloys). However, irons and steel alloys can also be cast in this method using graphite molds. Parts created via the gravity casting process include but not limited to:
- Gears
- Splines
- Gear Housings
- Pipe Fittings
- Wheels
- Fuel injection housings
- Valve and pump parts
- Glass manufacturing equipment parts
- much more
Gravity Casting Advantages
Some of the direct benefits that gravity casting provides include:
- High production rates
- Good part-to-part dimensional consistency
- Excellent soundness with low porosity and metal folds
- Cools faster, resulting in finer grain size than sand cast parts
- Reusable molds
- Directional solidification is easily induced
- Increased dimensional accuracy
DEECO Metal’s Gravity Casting Process
The gravity casting process consists of various steps: mold preparation, assembly, pouring, cooling, and opening. Once completed, the part within the mold is ready for use or secondary finishing services.
Mold Preparation
First, the mold is preheated to around 300-500°F (150-260°C) to allow better metal flow and reduce defects. Then, a release agent (refractory material or ceramic coating) is applied to the mold cavity surfaces to facilitate part removal and increase the mold life.
Mold Assembly
The mold normally consists of at least two parts - the two mold halves and any cores that form complex features. Such cores are typically made of iron or steel, but expendable sand cores are sometimes used. The cores are inserted in this step, and the mold halves are clamped together.
Pouring
The molten metal is poured slowly from a ladle into the mold through a sprue at the top. The metal flows through a runner system and enters the mold cavity.
Cooling
The molten metal is allowed to cool and solidify in the mold.
Mold Opening
After the metal has solidified, the two mold halves are opened, and the casting is removed. During cooling, the metal in the runner system and sprue solidify. Any material attached to the casting is cut off, and any excess material is removed.
What is the Difference Between Gravity Casting and Sand Casting?
The main differences between these casting methods lie in the mold and structure. Sand casting is accomplished by shaping a mold from a sand mixture and pouring molten liquid metal into the cavity in the sand mold. The mold cools until the interior metal has solidified. It is essentially an expendable sand mold casting process since the sand mold is destroyed after its initial use. Additionally, sand casting allows smaller batches to be made compared to permanent mold casting, designed for larger runs.
Conversely, gravity casts can be used repeatedly to make identical parts. This reusable mold casting is beneficial for applications requiring numerous production runs of the same part. The initial investment costs are a bit higher than sand cast patterns, but the costs generally make up for themselves due to the extended usage factor.
DEECO Metals will work with you to determine which casting method suits your project needs.
Why Choose DEECO Metals for Your Permanent Mold Casting Needs?
DEECO Metals is more than a custom metal part supplier to OEMs in North America. We pride ourselves on providing high-quality finished metal parts and assemblies at competitive prices. We also offer value-added services such as surface coatings or sub-assembling to reduce risk and save money.
Our one-stop metal shop saves you time and money. We also offer additional cost savings to our returning customers when they consolidate their inventory and product needs through DEECO. Additional advantages of teaming with DEECO Metals include:
- Full Technical Support
- Warehousing with JIT Stocking Programs
- Sales Support
- Fixed Order Pricing
- Assembly Services
Create Your Parts with Gravity Casting from DEECO Metals Today
DEECO Metals provides 38 years of gravity casting part manufacturing experience with small, medium, and large mill run production capabilities. Contact us regarding our permanent mold casting production capabilities, or request a quote for direct pricing information today.